I reviewed several write-ups on the subject that I found via google, and the article Steve sent
me that Whit wrote - the latter was particularly helpful. Basically what this amounts to, is using light gauge wire in a deliberate short circuit, paying careful attention to the gauge, length and
resistance of the wire, so we plan the watts it will consume as it tries to pass all the current it can and inevitably heats up. The choice of wire is thus very important. We need it to be
insulated so we don't get unplanned short circuits, and the insulation needs to be very heat resistant. We need it to be multi-stranded so it doesn't fatigue and break from flexing - the
more strands the better. We need consistent quality in the wire so impedance is constant (no one place has too high impedance and heats up too much) and predictable.
Whit's recommendation is perfect. mil-spec 28ga 19/40 stranded silver plated copper with teflon coating. The teflon is good to 392° f and is slippery which enables sewing with it, and the
high strand count makes it very durable in a flex application, while the mil-spec ensures uniformity.
Whit had written up a great article on this subject, and had determined this wire meters at 0.068ohms / ft. He wired his so he could select via a switch, to run power through 100 ft of this
wire yielding 6.8ohms, at 13 volts that results in 1.85 amps and 25 watts. Running the current through only 50 ft halves the resistance to 3.4ohms and yields 3.7amps and 50 watts assuming 13 volts.
There's an ohm's law calculator at
http://ourworld.compuserve.com/homepages/Bill_Bowden/ohmslaw.htm
I decided I wanted to shoot for a little extra capacity since I planned to throttle it down anyway
with the digital control. The clothing makers typically make their jackets around 50-70watts. I got 85watts assuming 13 volts (meters at 2.0-2.1ohms) by using 2-57ft lengths of wire, each
meters at 3.8 ohms, connected in parallel.
You need a pleated jacket to help hold the wires from moving around. The wires need to be run
just inside the lining, inside any insulation (The Dickies jacket - made in Egypt - has polyester fill). I discovered it is best to NOT break the quilting stitches but to poke the big needle through the
inner lining, go around the stitching, then poke it back inside the lining. I found out the hard way that if you just ram it through the stitches, the pleating will unravel.
I made two giant needles out of steel dowel - one is 3/16" diameter, the other 1/4". I used the bigger one to route heavy wire (extension cord) from the input plug on the right side bottom of
the jacket, to the plugs at the end of the sleeves, for the gloves. Unfortunately I pushed it through the pleat stitches and they are unravelling. Well I found out that was a mistake, you can
avoid. Now I would just route it on the inside of the jacket and stitch it in place every 4 inches or so.
Figure out the watts you want, use the above calculator to determine what length wire will produce that at the rate of .068ohms/ft, and use the pleats of your jacket to carefully route the
wire evenly so you run out of wire when you run out of area to heat. Jason mentioned in his article that it's best to avoid heating your shoulder blades as they are bony and the heat
conducts too easily there, whereas you do want plenty of heat on your kidney area. Remember adding wire in series increases the impedance and thus a longer wire will use less watts and
produce less heat, while wires in parallel will lower impedance, increasing power use and heat.
On the heat control - I bought mine at
http://www.warmnsafe.com. This company made the heat control for Gerbing - until Gerbing got tired of paying their price and reverse-engineered
the controller to get the schematic, then outsourced it to China, thereby ripping off Mike's intellectual property, knowing he didn't have the resources to sue them. I've had my
TromBones patent infringed by 2 Dutch companies - it turns out having a patent and enforcing it are two different things - my lawyers want a quarter-mil retainer to go after them. He who has
the most bucks wins. Anyway, I'm really pleased with the controller and the coax connectors I got from Mike, and his customer service is Johnny-on-the-spot.
The big needles - they need to be sharp and smooth. I ground the profile of the point against the side of my chop saw, but any power grinder or sander would work. Then I smoothed the
profile with my 1" belt sander (no platen), and smoothed the surface so it would slide easily through the fabric, by turning it against the cloth side of the sanding belt. I drilled the needle
eye with a small drill and put a couple grooves from the eye to the end with a dremel cutter wheel. You use it just like a sewing needle - the wire is run through the garment double thick, so
the current will go out and back in series. I made the bigger needle with the hollow end and the set screw to route the extension cord - that wasn't the best plan, just stitching it inside the
garment would be better. If you use switches to select the wires to use them in parallel rather than series, it will double the power and heat. As for me, I wanted it simple and just bought the
controller.
I wired mine so the current for the jacket is connected on the bottom hem left side. From there
it splits to two circuits. One goes up and down on every pleat on the front, then routes into the sleeve, goes down to the wrist on the inside, up, down, and back up with 3 lines covering the
inside and top and one on the back. This seems to work well. Then the circuit covers the left half of the back except the shoulder blade, and covers up the spine to the collar. The other
circuit goes around the bottom hem to the right back, covers the lower back only, then does the right sleeve in the same manner as the left, then the right front is last in the same manner as the left.
Here's some pictures I took, mostly self-explanatory, all link to enlargements:



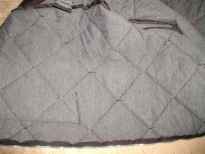


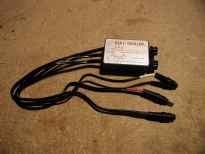
Here's the Article Whit Brown wrote:
HOME BREWING A HEATED LINER - V1.1
My leather Kilimanjaro jacket has a full, snap-in, Thinsulated
liner. While it does make things a good bit warmer, I thought I'd
try to improve on that by electrification. The liner is silk on both
sides of the Thinsulate filler and vertically stitch/pleated in
1-1/4" channels. The process described below could also be adapted
to other thin, lightweight, garments readily available at WalMart, Cabela's or
outdoor stores.
I used a hundred feet of mil-spec, silver-plated, Teflon covered, 28
ga, stranded wire to act as the 'elements'. I could have used
conventional PVC-covered wire, but I wanted the extra margin of
temperature protection and longevity. The Teflon covered stuff is
good to 392 degrees (F). It is quite flexible, nearly indestructible
and quite slick so it pulls easily through fabric.
I made a 'needle' out of an 1/8" dowel about 24" long. One end
semi-pointed, the other with a small hole as the 'eye'. After
unwinding the 100' roll I threaded the 'needle' at the 50' half
point which left me with the needle pulling two 50' lengths of wire.
I recommend the initial entry and final exit to be on the outside of
the liner around the lower left-hand corner. This keeps any underway
switching and plugging/unplugging confined to the non-throttle hand.
I then proceeded to thread these two conductors through the 22 pleats
that made up the 'body' of the liner, I also made four runs through
each full length sleeve, trying to avoid the armpit area. Remember
to anchor about 3" of the two ends exposed at the entry point, or
you could just connect these two ends to the terminal strip now.
One can pierce the silk material with the pointed end, run it up
through a channel to the top of the garment, then pierce your way
out of that channel. Once the 'needle' and wire is a couple feet
outside that channel, you can then reinsert the needle's point back
into that same exit hole and go across, through the adjacent
channel's stitching, enter the next channel and come back down, etc.
This leaves no exposed wiring while transiting the pleat's
stitching. The piercing holes in the silk close up almost completely
on their own.
When threading, make sure you keep the wires on the 'inside' of the
liner, between the inner silk lining and Thinsulate filler, if
applicable. (The outer surface of the Thinsulate has a metallized
foil and I don't think the wire would transfer much heat through the
filler to the body.) After all the threading, I exited the liner at
the same point of the original entry. I then separated the half
point that was in the eye of the needle. This results in four ends
of the two paralleled 'elements'. Make sure you mark the ends to
keep them paired either beforehand or use an ohmmeter to mate them
up afterwards. You'll need to be able to identify each end of the
two sections. Actually, one could carefully remove about 1/2" of
insulation at the wire's mid point (where the "needle's eye" was),
and connect this to the center terminal of the terminal strip.
This center point and two ends are terminated to a small laced-in,
barrier terminal strip (RatShack 274-658), on the outside of the
liner, so it lives between the liner and outer jacket on the lower,
front, left side when worn. The other side of this terminal strip is
tied to the 4" 3-conductor, 16 ga cable. Any good, flexible
appliance or extension-type cable will work. Some of these cables
are available with a silicon jacket which remain very flexible even
in cold weather. This short cable goes to the 'male' 3-conductor,
inline connector. I recommend the "Cinch" series connector as it has
plenty of contact area yet will disengage readily if you forget and
walk away while still connected. This concludes the jacket wiring.
The mating 'female' end of the Cinch connector goes through a
convenient length of the same type 16 gauge, 3-conductor cable as
detailed above. It needs to be long enough to go from the
rider-mounted jacket's male plug to the switch, wherever you put it.
It is recommended you incorporate some sort of cable clamp or
'strain relief' close to the switch so the switch, itself, won't
have to take any unexpected jerks from the cable.
The input-side of the switch goes through the necessary length of 16
ga, two-conductor cable to the battery or preferably to a switched
accessory relay via a 10 amp inline fuse holder (#270-1213) and ATC
blade fuse as close to the relay "out" terminal as possible.
For information only, and for those not fluent with electro-speak,
note the transition of the 28 ga Teflon wire to the larger 16 ga
supply wire at the jacket's terminal strip junction. Wire, the size
of 28 ga (.013" diameter), with its inherent greater resistance,
ceases being a low-loss conductor and morphs into a 'heating
element' like an electric blanket. The supply-side (love that term)
16 ga (.051" diameter) will readily carry this current with little
loss (heating effect) so anything smaller beyond the 16 ga wire will
heat up, relatively, while trying to keep supplying the source
voltage and current. This is, in effect, a calculated short circuit.
The reason I elected to pull TWO lengths of wire throughout the
liner was to take advantage of the combined series switching
possibilities yielding two separate heating wattages, thus
eliminating the big resistor. (Actually three heats are possible by
switching in a paralleled configuration yielding 100 watts, but I
found this amount of heat to be too much and the necessary 4P3T
switch is very hard to find. It would also necessitate a separate
on-off switch) 100' of this wire exhibits 6.8 ohms resistance. When
the 13 volts runs through the full length (both 50' elements in
series via the switch) it pulls about 1.85 amps yielding ~25 watts,
the low position. When the 13 volts runs through only one of these
two elements (via the switch), the resulting 3.4 ohms pulls 3.7
amps, yielding ~50 watts, the high position.
Lastly, I strongly recommend the DPDT, center off, switch be the
waterproof "marine" type switch with the sealed entry barrel where
toggle bat enters. I have the necessary teflon wire, marine switches,
connectors and terminal strips.
Whit Brown